Największa spycharka Europy
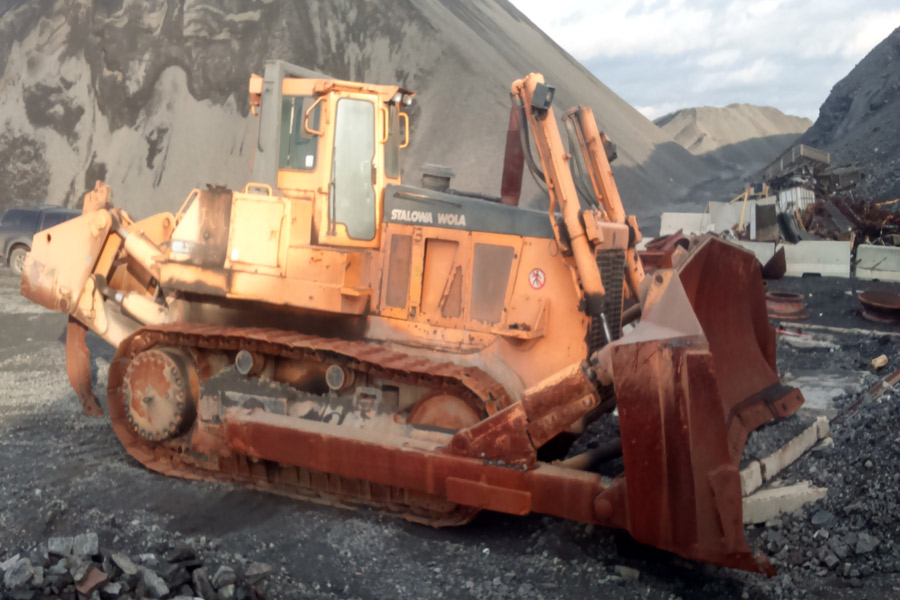
W latach 80 Huta Stalowa Wola rozpoczęła produkcję jednych z największych na świecie, blisko 70-tonowych spychaczy.
Lata sześćdziesiąte przyniosły poważną rozbudowę energetyki oraz towarzyszących im kopalń węgla brunatnego. W tamtym dziesięcioleciu rząd zbudował Turoszów, Konin, w planach pojawił się Bełchatów. Na szczeblu Rady Wzajemnej Współpracy Gospodarczej, czyli ciała koordynującego poczynania gospodarcze krajów podbitych przez ZSSR, przygotowywano rozbudowę górnictwa surowcowego, a także towarzyszącej im infrastruktury, w tym rurociągów. Do realizacji tych ambitnych planów niezbędne były ciężkie maszyny, w tym wielkie spychacze. Początkowo Polska, podobnie jak pozostałe kraje satelickie ZSSR, kupowała maszyny za granicą, za twarde dewizy, jednak na dłuższą metę było to zbyt kosztowne. Na dodatek dotychczas produkowane w krajach RWPG maszyny budowlane okazywały się zbyt mało wydajne w porównaniu do zachodniej konkurencji, a technologia ich produkcji droga. W rezultacie w Moskwie zapadła decyzją o modernizacji przemysłu maszyn budowlanych całego obozu, a spora część inwestycji przypadła na Polskę, jako kraju specjalizującym się w tym asortymencie wśród państw RWPG.
Giganty z Chicago i Stalowej Woli
Ciężkie spychacze produkowane były przez japońską firmę Komatsu oraz amerykańskie: Caterpillar, Allis Chalmers a także International Harvester Company (IHC). Właśnie ta ostatnia firma wyraziła zainteresowanie współpracą z Polską. Po wielomiesięcznych negocjacjach obie strony podpisały 6 lipca 1972 roku w Chicago (gdzie mieściła się siedziba IHC) porozumienie licencyjne.
Ze strony polskiej umowę zawierało Zjednoczenie Maszyn Budowlanych Bumar, zaś samo podpisanie umowy odbyło się obecności m.in. przedstawiciela Ministerstwa Przemysłu Maszynowego i konsulatu handlowego PRL w Chicago.
Polska uzyskiwała prawo do produkcji ładowarek gąsienicowych 175C o pojemności łyżki 1,5 m3 i spycharek gąsienicowych: TD-15C o mocy 140 KM, TD-20C i następców tej konstrukcji, o mocy 170-200 KM oraz TD-25 wyposażonych w 285-konne silniki. Maszyna TD-25 została zakupiona także w wersji układacza rur.
Wytwarzanie spychaczy Zjednoczenie Bumar powierzyło Hucie Stalowa Wola, której konstruktorzy wkrótce po podpisaniu umowy przyjechali do Chicago przejąć dokumentację i wiedzę technologiczną licencjodawcy. Montaż pierwszych maszyn gąsienicowych IHC w Stalowej Woli ruszył w drugiej połowie 1973 roku.
W podkarpackim zakładzie rozwinęła się produkcja ładowarki gąsienicowej 175C (w ofercie przetrwała do 1999 roku), spycharki gąsienicowej TD-15C (produkowanej do 2000 roku) i TD-25C, która utrzymała się w produkcji do 1985 roku. Układarka do rur TD-25CS pozostała w produkcji do 1980 roku. HSW eksportował także komponenty do brytyjskiej fabryki IHC w Doncaster, spłacając licencję i koszty zakupu wyposażenia zakładu. Brytyjski zakład specjalizował się w wytwarzaniu spycharki TD-15C i ładowarki 175C.
IHC od samego początku stawiał wysokie wymagania jakościowe. Założył, że zarówno gotowe wyroby jak i części z HSW mają być nie do odróżnienia od oryginalnych. Amerykanie nie stosowali taryfy ulgowej, byli bezlitośni. HSW spełniła jednak postawione wymagania.
Przedstawiciele Harvestera byli na tyle zadowoleni ze współpracy z HSW, że zgodzili się na poszerzenie współpracy o jeszcze cięższe spycharki TD-40 o mocach do 500 KM oraz TD-50 wyposażone w 750-konne silniki. Porozumienie, podpisane 5 września 1975 roku, objęło także najcięższe układarki do rur SB-85 o udźwigu stu ton.
Najcięższe modele były dopiero na deskach kreślarskich. Pracownik HSW Marek Stańkowski wyjaśnia, że TD-40 to konstrukcja amerykańsko-polska, zaprojektowana w systemie metrycznym, a nie w calach i stopach, które obowiązują w USA.
Silniki do najcięższych spychaczy
Razem z licencją na spychacze, Polska kupiła także prawa do produkcji silników, które miały napędzać te ciężkie maszyny. Przygotowaniem i produkcją silników zjednoczenie obarczyło Zakłady Mechaniczne im. Nowotki na warszawskiej Woli.
Założone na początku lat 50 do produkcji silników czołgowych, wypuszczały długie serie tych jednostek z aluminiowymi kadłubami w wersji 12- i 6-cylindrowej, także w odmianach cywilnych. Od końca lat 60 ZMiN produkował także na licencji firmy Henschel silniki 12- i 6-cylindrowe z żeliwnymi kadłubami do zastosowań stacjonarnych. Zakład dysponował największą w Polsce odlewnią aluminium i dużą żeliwa.
ZMiN wysłał do Chicago kilkuosobową grupę konstruktorów, której przewodniczył Stefan Wasiukiewicz. Członek jego zespołu, Lubomir Kossowski wspominał, że z początkiem 1976 roku rozpoczęła się współpraca konstrukcyjna. – W praktyce chodziło o wykonanie w Polsce prototypów silników, których dokumentację opracowano w USA – wyjaśnia Kossowski. – W rzeczywistości wyglądało to tak, że konstrukcja silnika została opracowana w USA, natomiast Polacy mieli pewien wpływ na szczegóły konstrukcyjne i postać dokumentacji – opisuje Kossowski. Wówczas po raz pierwszy Polacy zetknęli się z wykorzystaniem programów komputerowych w projektowaniu silnika, a później w ich badaniu. – Był to zupełnie inny świat zwłaszcza, że w tym czasie w Polsce kalkulator elektroniczny był czymś niezwykłym – podkreśla konstruktor.
- Współpraca polegała przede wszystkim na ciągłej, nieraz codziennej łączności teleksowej, pocztowej, a także na stworzeniu w USA stałej, kilkuosobowej placówki polskich konstruktorów, wymienianych co 2-3 miesiące, będącej też we własnym kontakcie z zakładem w Polsce – opisuje Kossowski. Dodaje, że przez pierwsze tygodnie Amerykanie nie wpuszczali polskich konstruktorów na hale produkcyjne, choć zwiedzali je polscy oficjele z ministerstwa lub dyrekcji fabryki. – Dopiero po trzech tygodniach pobytu, gdy znowu przyjechał z Polski dyrektor i po zwróceniu się nas, konstruktorów, do niego, Amerykanie zorganizowali dla nas wycieczkę. Z Amerykanami mieliśmy dobre kontakty, również prywatne, i oni, jak zwykle szczerze wyjaśnili, że dygnitarze zwykle się nie znają, więc można im wiele pokazywać – z uśmiechem wspomina Kossowski.
Kwadratowa moda
IHC opracowało rodzinę silników 165 o mocy 100 KM z cylindra. Oznaczenie 165 odnosiło się do średnicy cylindra w milimetrach. Dokładnie było to 165,1 mm, bo wyjściowym wymiarem było 6,5 cala. Amerykanie przygotowali całą dokumentację w układzie metrycznym. – Zdarzały się pewne śmiesznostki, ponieważ przyzwyczajeni do układu calowego konstruktorzy amerykańscy, zwłaszcza starsi, podawali czasem wymiary milimetrowe z ułamkami do szóstego miejsca po przecinku, tak jak przy calach. Jednak współpraca układała się dobrze – zapewnia Kossowski. – Ważną zaletą Amerykanów było nazywanie rzeczy po imieniu, czyli szczerość. Gdy popełnili błąd otwarcie przyznawali, co u innych zagranicznych współpracowników nie zawsze się zdarzało – podkreśla polski konstruktor.
Amerykanie przygotowali całą rodzinę silników od 6- do 16-cylindrowych, z wersjami widlastymi o rozchyleniu 90 stopni. Lubomir Kossowski ubolewa, że nawet w dziedzinie silników wysokoprężnych panują mody. Ulegli jej także Amerykanie, którzy zaprojektowali rodzinę IH-165 w tzw. układzie kwadratowym, w którym skok tłoka jest taki sam jak jego średnica. – W silnikach wysokoprężnych ten kierunek ma taką podstawową wadę, że ze względu na wysokie stopnie sprężania, komora spalania wypada bardzo niska, jest płaska jak naleśnik, podczas gdy ideałem (zwykle nieosiągalnym) jest kula.
Silniki IH-165 miały zatem skok i średnicę cylindra 165 mm, co dawało pojemność z cylindra 3,53 litra. Stopień sprężania sięgał 15:1, a więc był bardzo wysoki jak na turbodoładowany silnik. Każdy cylinder miał osobną głowicę, w którą wkręcony był pompowtryskiwacz, podający paliwo bezpośrednio do komory spalania. Wokół wtryskiwacza konstruktorzy rozmieścili cztery zawory wyposażane w obracacze.
Wyposażony w 3 pierścienie tłok poruszał się w grubościennej (ścianka o grubości 23 mm) mokrej tulei. Moc z cylindra wynosiła 100 KM (75 kW) przy 2100 obr/min przy bardzo wysokim maksymalnym ciśnieniu spalania, dochodzącym do 122 atm. Średnie ciśnienie użyteczne wynosiło 12,1 atm. Silniki wyposażone były w turbosprężarkę i chłodnicę powietrza doładowującego. Jednostki zostały przystosowane do pracy przy dużych przechyłach, typowych dla maszyn roboczych.
Pierwsze prototypy silników
Jako pierwszy przygotowywany był 6-cylindrowy, rzędowy silnik IH-165-6. Polsko-amerykańska umowa przewidywała wykonanie na Woli odlewów jednego z kluczowych komponentów silnika: kadłubów i montaż diesli.
Odlew kadłuba IHC był stosunkowo lekki dzięki zmniejszeniu grubości nieobciążonych ścianek. Niektóre miały tylko 6-8 mm grubości, gdy w Henschlu np. od 10 do 12 mm. – Odlew o różnych grubościach ścianek był możliwy dzięki zastosowaniu przez Amerykanów żeliwa niskostopowego – wspomina technolog ZMiN Michał Stachura.
Dodaje, że główny konstruktor IHC żądał na każdym wymiarze tolerancji +/- 0,8 mm co było bardzo trudne w przypadku mierzącego ponad metr długości bloku. – Byliśmy młodzi, do dyspozycji mieliśmy nieograniczone środki i ambicje i zrobiliśmy oprzyrządowanie do mającego 1,2 m długości kadłuba, którego tolerancje nie przekraczały +/- 0,8 mm. Normalnie tolerancje dla tak dużych elementów wynoszą 7-10 mm. Była to kwestia precyzyjnego wykonania rdzeni oraz ich kalibracji – wyjaśnia Stachura.
Z pierwszych ośmiu kadłubów sześć pojechało do USA, a dwa przez kilka lat służyły w wolskiej odlewni za podstawę przy obrabianiu kadłubów Henschli. – Ponieważ skrzynka powietrzna była odlewana z kadłubem, przypominał on sześcian i był bardzo stabilną podstawą – tłumaczy.
ZMiN poradził sobie z odlewami kadłuba, jednak żaden zakład w Polsce nie chciał produkować wałów korbowych. Były one kute, ale robota okazała się trudna; Amerykanie postawili wysokie wymagania materiałowe i wymiarowe i nikt, łącznie z Łabędami, tego w Polsce nie chciał się podjąć. Dla pierwszych silników zrobił je Mannesmann. Rosjanie, którzy byli największymi nabywcami licencyjnych silników Henschla, a w przyszłości także IHC nalegali, żeby je kontynuować, ale sami też nie byli w stanie odkuć wału korbowego.
Spychacze z poślizgiem
Prototypy trafiły na badania, lecz trudności technologiczne oraz gospodarcze sprawiły, że przyszłość programu stanęła pod znakiem zapytania. W państwowej kasie zabrakło pieniędzy na uruchomienie tej produkcji. Załogi polskich zakładów z kolei nie wyrywały się do wytwarzania nowego asortymentu, bo oznaczało to zazwyczaj więcej kłopotów niż korzyści.
Prototyp spycharki TD-40 powstał w latach 1978-79 roku. Jego pokaz odbył się w sierpniu 1979 roku. Był to pierwszy w Europie tak ciężki spychacz. Amerykanie byli bardzo zadowoleni z postępu prac i zgłaszali zapotrzebowanie na 250 tego typu maszyn rocznie.
Po stanie wojennym polsko-amerykańska współpraca w dziedzinie silników ustała. IHC pogrążona w kłopotach zarzuciła konstrukcję silników wielkich mocy, a w ZMiN dokumentacja silników trafiła do archiwum. Nadal jednak trwały prace na uruchomieniem produkcji najcięższych spychaczy, choć w okrojonym kształcie: obie strony zrezygnowały z maszyn TD-50.
Kłopoty finansowe zmusiły IHC do sprzedaży jesienią 1982 roku działu maszyn budowlanych koncernowi Dresser Industries i spowodowały spadek tempa prac nad spycharkami rodziny TD-40. Dyrekcja Dressera była nieufna w stosunku do HSW, producenta zza żelaznej kurtyny.
Pierwsze seryjne maszyny (5 szt.) zjechały z taśmy w 1984 roku, a więc z kilkuletnim poślizgiem. – Były i są produkowane tylko w Stalowej Woli, nigdy w USA – podkreśla Stańkowski.
Pierwsze TD-40 wyposażono w silniki IHC, ale od wersji B z 1989 roku zamiast silników International Harvester maszyny otrzymywały silniki Cummins. W 1997 roku do produkcji weszła wersja TD-40C. Moc silnika wzrosła z 460 w pierwszych spycharkach do 520 KM. Produkcja nie sięgnęła spodziewanych setek sztuk rocznie. W latach 80 niskie ceny energii zniechęcały do inwestycji w górnictwo energetyczne, głównego nabywcę dużych spychaczy. HSW wytwarzała od 20 do 50 spycharek TD-40 rocznie w zależności od zamówień.
Blisko 70-tonowy TD-40 pozostał flagowym produktem HSW, eksportowanym do Europy, Azji, Ameryki Północnej i Południowej. Spycharka do tej pory cieszy się dobrą opinią użytkowników.
Tekst: Robert Przybylski
T&M nr 5/2016