Chude lata 80.
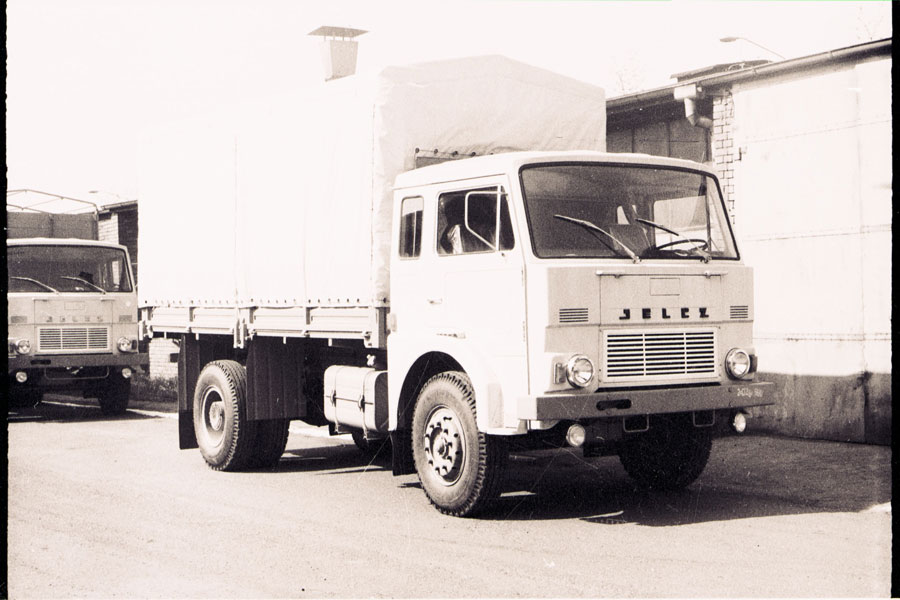
Pracownicy tczewskiej fabryki wspominają dekadę lat 80. jako szary i bezbarwny okres, gdy brakowało rąk do pracy i dewiz na import części zamiennych oraz komponentów do produkcji.
W 1985 roku fabryka obchodziła 40-lecie i z tej okazji wybiła pamiątkowy medal „Zasłużony pracownik Fabryki Przekładni Samochodowych Polmo Tczew”, wręczany pracownikom podczas wrześniowych uroczystości. – Wyliczyłem wtedy, że byłem 22 dyrektorem. Czyli odliczając moje 4 lata, na dyrektora przypadały niecałe 2 lata urzędowania – podsumowywał dyrektor naczelny Józef Łodej.
Akord i racjonalizatorzy
Częste zmiany dyrekcji wynikały z niewykonywania przez zakład planów, a brak skrzyń biegów uniemożliwiał wywiązanie się z zobowiązań fabrykom samochodów. – Produkcja była bardzo zaawansowana technicznie i skomplikowana, stąd liczne problemy. Natomiast przy produkcji starego asortymentu, sytuację utrudniały liczne awarie maszyn, jeszcze pamiętających Starachowice. Skrzynie A25 wytwarzaliśmy na starych maszynach, z których wyciekały olej i chłodziwo. Na liniach produkcji licencyjnej pracownicy bardziej dbali o ład i porządek – podkreślał dyrektor.
Jeden z pracowników Działu Głównego Mechanika, który odpowiadał za remonty maszyn wspomina regularne przeciążanie obrabiarek. – Gdy pracowałem u mechanika, widziałem dużo wyeksploatowanych maszyn, które trzeba było odtwarzać – przyznaje.
Opisuje rewolwerówkę, która była wykorzystywana tylko do wiercenia otworów jednej średnicy. Co pół roku musiał wymieniać w niej wszystkie śruby pociągowe, bo miały nadwyrężone gwinty. Maszyna została dobita przez przeciążenie. Co prawda były odbiory produkcji, badania cichobieżności, ale odpowiedzialność na stanowisku pracy była iluzoryczna. Kontrolerzy jakości dopuszczali do sprzedaży wyroby wykonane z tolerancjami większymi niż dopuszczała dokumentacja. Dociążenie maszyn brało się z produkcji na akord: żeby zarobić, robotnicy musieli przekraczać normy i to się odbijało na maszynach. Ludzie od normowania pracy byli znienawidzeni w załodze.
Czasami zatrudnionym udało się dorobić wnioskami racjonalizatorskimi. Przedstawiciel Działu Głównego Mechanika wspomina, że jeden z pracowników odchodząc z tczewskiej fabryki zgłosił wniosek racjonalizatorski. Po przeczytaniu wniosku technolodzy stwierdzili, że to niemożliwe. Jak nie, skoro robię tak od kilku lat? To dlaczego pan dopiero teraz to zgłasza? Bo odchodzę na emeryturę i chciałbym zarobić jeszcze kilka złotych.
Byli pracownicy przyznają, że zakład nie miał popularności na rynku pracy. Brakowało chętnych, mimo że fabryka powołała Zespół Szkół Zawodowych Polmo w Tczewie (obchodził 25-lecie 14 października 1987 roku). Fluktuacja kadr była duża, zawsze brakowało ludzi, a szczególnie trudne warunki panowały w zakładowej odlewni. Brak rąk do pracy zmusił dyrekcję do zatrudnienia na linii obudów sprzęgła więźniów ze Sztumu. Na wygrodzonym siatką fragmencie hali obrabiali ten jeden z najprostszych detali.
Wykruszała się także kadra techniczna, której płace zmalały w stosunku do wynagrodzeń robotniczych. Już na początku 1982 roku wiceminister pracy, płacy i spraw socjalnych Józef Bury w rozmowie z Ireną Scholl z Dziennika Bałtyckiego przyznawał, że „w 1970 roku przeciętna płaca pracownika inżynieryjno-technicznego była o 50 proc. wyższa od robotniczej, dziś jest wyższa o 20 proc., zaś administracyjno-biurowa była wyższa o 3 proc., a dziś stanowi 82 proc. przeciętnej płacy robotniczej. (…) Nie wolno doprowadzić od nadmiernego spłaszczenia struktury płac, gdyż zatraciłoby się motywacyjną funkcję płacy.”
Z upływem lat poprawa nie następowała i szczególnie młodzi inżynierowie odchodzili z przemysłu, często trafiając do handlu, gdzie zakładali popularne w tamtych latach warzywniaki. Przykładem może być Tadeusz Wilczarski, który pracował w dziale rozwoju FPS i w połowie 1984 roku przeszedł do pracy w Stowarzyszeniu Naukowo-Technicznym NOT w Gdańsku. – Miałem bardzo niskie wygrodzenie i w fabryce na wyższe nie mogłem liczyć. Gdy zmieniłem pracę, mój nowy pracodawca dał mi na początek ponad dwa razy wyższą pensję niż miałem w FPS – podkreśla Wilczarski.
W dekadzie ograniczeń dewizowych, trudność z utrzymaniem ruchu miał również Dział Głównego Mechanika. W halach przeznaczonych do produkcji licencyjnej 35-40 proc. maszyn pochodziło z obszaru dewizowego (Niemcy, Szwajcaria), dla nich dostęp do części zamiennych był poważnie utrudniony. Raz na rok można było złożyć zamówienie na części zamienne, co oznaczało zarezerwowanie dewiz. Mechanicy zgadywali co może zepsuć się i kupowali, ile się dało szybko zużywających się części jak łożyska i wrzeciona. Na te ostatnie, z uwagi na sposób eksploatacji i tak brakowało dewiz, więc trzeba było odtwarzać je na podstawie dokumentacji, dla której wzorem były zużyte części. Na obrabiarkach Głównego Mechanika pracowali najlepsi fachowcy.
FPS dysponował potężną służbą utrzymania ruchu, gdzie na wydziale mechanicznym robiono remonty kapitalne wysłużonych obrabiarek. Do nich dorabiano części zamienne według dokumentacji przygotowanej przez inżynierów FPS, co zresztą było typowe w polskich warunkach. Zakłady we własnym zakresie odtwarzały elementy hydrauliki siłowej, pneumatyki, części mechaniczne.
Jeśli nawalił układ hydrauliczny różniczkujący, Rexroth czy Parker, a nie było takiego, który by pasował, trzeba było odtwarzać część samemu. Ponar Żywiec miał licencję Roxrotha, ale jedynie na ograniczoną liczbę zaworów.
W przypadku dostaw krajowych, kwitł handel wymienny. Gdy pewnego razu ktoś ukradł silnik wentylatora, mechanik z FPS pojechał do Malborskiej Fabryki Wentylatorów. Tam składał zamówienie i słyszał: za rok może będzie. Nie pomagały tłumaczenia, że Sanepid zamknie wydział. Producent rozkładał ręce „Nic nie zrobimy”. Dopiero gdy usłyszał, że chodzi o FPS, poprawiał się: „to trzeba było tak mówić”. Pracownik działu zbytu malborskiej fabryki dzwonił do działu transportu, wręczał listę potrzebnych im części, za dwa dni pracownik FPS Tczew przywoził je i wracał z kompletnym wentylatorem.
Jelczańskie rozterki
Najważniejszym odbiorcą FPS były Starachowice, które zaopatrywały wojsko w modele szosowe i terenowe. – Skrzynie S5-45 dla wojska robione były na jednej linii, ale odbiór części prowadzili na wydziałach pracownicy wojskowego przedstawicielstwa, którzy stawiali pieczątki na częściach. Z nich była montowana partia skrzyń dla Starów 266 i w całości sprawdzana na hamowni. Te partie liczyły po kilkadziesiąt, może po sto sztuk, w miarę zapotrzebowania bieżącej produkcji – zaznaczał Łodej.
Poza Starachowicami tczewski zakład miał dwóch głównych klientów: Jelcz i Autosan. Mniejsze ilości przekładni kupował Bumar. FSC i JZS regularnie oskarżały Tczew o brak skrzyń biegów i spowodowane tym niewykonanie planów. – Żeby uniknąć takich oskarżeń miałem w Starachowicach i Jelczu swoich ludzi, którzy kontrolowali, ile przekładni jest u każdego z nich. Każdy z nas borykał się z tymi samymi problemami spowodowanymi mi.in. nieregularnymi dostawami. Tczew nie dostawał na czas odkuwek z FSC Lublin, ze Skoczowa, brakowało różnych części, łożysk. Np. łożyska do S6-90 były importowane i z tego powodu skrzynia produkowana była w niewielkich ilościach dla Jelcza i Bumaru. Z kolei gromadziły się nadmierne zapasy niechodliwych części. Mieliśmy nieustanny problem z bankami właśnie z powodu nadmiernych zapasów magazynowych – wspominał dyrektor FPS. Innym wyrobem, który przez całe lata nie mógł pojawić się w produkcji był multiplikator GV90, łączony z przekładnią S6-90, choć przygotowania do jego wytwarzania zostały ukończone w czasach PRL. – Zlokalizowano produkcję i obróbkę odlewów, samodzielnie wykonywano elementy układu przeniesienia mocy oraz układu przełączania multiplikatora. Przełączanie aktywowane było siłownikiem pneumatycznym WABCO-Westinghouse. Ten podzespół wymagający wydatków dewizowych prawdopodobnie limitował produkcję multiplikatorów. W odniesieniu do skrzyni biegów dodatkowo dochodziły problemy z łożyskami, uszczelniaczami, włącznikami i przegubami kulistymi, które do czasu lokalizacji produkcji w kraju pochodziły także ze strefy dewizowej – dodaje konstruktor skrzyń biegów Bogusław Postek.
Dyrektor przyznawał, że najlepiej, gdyby FPS zostało kombinatem. – To było jednak niemożliwe, bo wszystkie odlewnie i kuźnie z których korzystaliśmy należały do większych od naszego zakładów. Byliśmy zbyt mali, żeby stworzyć niezależną grupę – przyznawał Łodej. Skromne możliwości dewizowe hamowały produkcję licencyjnych skrzyń S6-90 dla Jelcza, który nie mógł rozwinąć produkcji ciężarówek serii 410. W tej sytuacji dolnośląski zakład zaproponował, aby Tczew przystosował do podowozi Jelcz serii 410 skrzynię 316 stosowaną w Jelczach 320.
Tczewski zakład odpowiedział pod koniec maja 1986 roku, że taka propozycja nie ma sensu. Po pierwsze przekładnia 316 ma „przestarzałą konstrukcję”, co skutkuje niską trwałością i niskimi walorami eksploatacyjnymi (mała liczba biegów, niedostateczny zakres przełożeń i stopniowanie biegów).
Po drugie wzrost produkcji 316 mógł odbyć się tylko kosztem wytwarzania bardziej poszukiwanych skrzyń licencyjnych. Powodem był zużyty park maszynowy zgromadzony dla wytwarzania skrzyń 316. Ich detale coraz częściej były obrabiane na maszynach zakupionych przy okazji licencji ZF. „W związku z powyższym zdolność produkcyjna 316 zmniejszyła się znacznie i wzrost produkcji w tych wyrobach również wymaga nakładów inwestycyjnych na zakupy maszyn dla likwidacji wąskich przekrojów.” FPS mogła produkować rocznie do 4 tys. skrzyń typu 316.
W tym samym roku tczewski zakład przystąpił do produkcji S6-90 o przełożeniu nadbiegu 0,81, które także było przewidziane przez licencjodawcę. Postek tłumaczy, że wdrożenie do produkcji nadbiegu 0,81 wynikało głównie z częstych uszkodzeń koła zębatego szóstego biegu w wersji z nadbiegiem 0,7. – Koło to miało stosunkowo niewielką średnicę zewnętrzną skutkującą bardzo cienką piastą, w której otwór wewnętrzny dyktowany był wielkością złożenia igiełkowego łożyskującego to koło na wałku głównym skrzyni biegów. Dodatkowo od dna wrębów uzębienia poprzez cienką piastę przechodziły otwory doprowadzające olej do złożenia igiełkowego. Powodowało to podczas pracy koła znaczne spiętrzenie naprężeń w piaście, inicjację pęknięć i w rezultacie rozrywanie piasty. Ten problem dotyczył głównie pojazdów jeżdżących długo na najwyższym biegu, czyli pojazdów eksploatowanych na dalekich trasach. ZF również miał problemy z trwałością tego koła, by je zminimalizować wprowadził wymóg zaokrąglania krawędzi otworów olejowych poprzez ich dogniatanie – było to rozwiązanie trudne technologicznie – przyznaje Postek.
Dodaje, że w 1990 roku w dokumentacji tczewskiej wprowadzono zmianę konstrukcyjną eliminującą otwory smarujące. Ponadto Jelcz w pojazdach z kabinami stałymi stosował tczewskie mechanizmy zmiany biegów, produkowane na licencji ZF. – Mechanizmy te były również stosowane w prototypach posiadających kabiny odchylane. W pojazdach tych był pokaźny otwór w podłodze kabiny, przez który przechodziła dźwignia zmiany biegów na stałe związana z ramą – opisuje Postek.
Opracował on 2-krzyżakowy mechanizm zmiany biegów. – Proces uzyskania ochrony trwał kilka lat, ale już do 1984 roku wykonanych zostało w Tczewie 80 takich mechanizmów. Produkcja w niewielkich ilościach trwała aż do czasów pojawienia się Eaton w Tczewie. Mechanizmy z tej rodziny dostarczane były do Jelcza i do Sanoka – wymienia konstruktor.
Kaktus na dłoni
W połowie lat 80. powstała skrzynia TS9-160 z planetarnym (obiegowym) zespołem zmiany zakresu przełożeń. – Ten zespół został w 1985 roku wprowadzony do TS8-120 dając TS8-121 oraz do TS16-140 dając TS16-141. Dodatkowo w tych skrzyniach biegów z uwagi na konieczność dobrego smarowania zespołu zmiany zakresu przełożeń (przekładni planetarnej) zastosowano układ smarowania wymuszonego z mimośrodową pompą olejową osadzoną na wałku napędowym – opisuje Postek.
Dodaje, że układ sterowania wewnętrznego (reduktora i skrzyni podstawowej) bazował na maksymalnej liczbie części już uruchomionych w ramach licencji i nie był optymalny. – Zdawaliśmy sobie sprawę, że każdy nowy element o nowej konstrukcji to problem z (potencjalnym) wdrożeniem do produkcji seryjnej. Stąd „niedoskonałość” skutkująca pewnymi ograniczeniami. Patenty były swego rodzaju zamknięciem prowadzonych prac konstrukcyjnych i wykonanych testów. Wymyślenie rozwiązania, wykonanie dokumentacji, wykonanie części, zbudowanie prototypu i wreszcie wykonanie prób zabierało dużo czasu - szkoda było odłożyć to tylko na półkę – wyjaśnia Postek.
Zbudowanie skrzyń z planetarnym reduktorem było sporym sukcesem fabryki. – Problem stanowi liczba warunków konstrukcyjnych, które należy spełnić by koło o uzębieniu wewnętrznym dało się poprawnie wykonać i by poprawnie współpracowało z satelitami.
Problemem jest również prawidłowe przeprowadzenie obróbki cieplno-chemicznej, by koło o uzębieniu wewnętrznym (koło pierścieniowe) nie uległo deformacji – wskazuje Postek.
W rezultacie wątpiących w pomyślne wykonanie planetarnych reduktorów nie brakowało. Odpowiadający za seryjną produkcję kół zębatych p. Witerski stwierdził, że „prędzej mu kaktus na dłoni wyrośnie niż fabryka zdoła wyprodukować potrzebne koła”.
Wszelkie narzędzia przygotowywał Dział Konstrukcji Narzędzi i Oprzyrządowania funkcjonujący w ramach Działu Głównego Technologa. – W Służbie Technologicznej zajmującej się przygotowaniem do nowej produkcji i nadzorem nad bieżącą produkcją pracowały ok. 42 osoby. W tym gronie byli konstruktorzy z Działu Konstrukcji Narzędzi i Oprzyrządowania do produkcji, a także sekcja zajmująca się powielaniem dokumentacji technicznej na potrzeby fabryki i archiwum dokumentacji technologicznej. W zakresie działania komórek typowo technologicznych było również typowanie urządzeń i obrabiarek do produkcji nowych wyrobów i modernizacji parku maszynowego, a także udział w procesie inwestycyjnym, w tym rozmowy z dostawcami urządzeń i konkretyzowanie parametrów technicznych obrabiarek i oprzyrządowania do nich. Poza Służbą Technologiczną, także Służba Narzędziowa miała swoją Sekcję Technologiczno-Konstrukcyjną liczącą ok. 7 osób, podobnie Służba Utrzymania Ruchu też miała Dział Technologiczno-Konstrukcyjny mający ok. 6 osób – wylicza ówczesny technolog obróbki cieplnej Ryszard Bartnik.
Dodaje, że w tym okresie raczej nie rozbudowywano zaplecza technologicznego, gdyż następował powolny spadek produkcji i nie było znaczących nowych uruchomień, które wymuszałyby rozbudowę parku maszynowego. – Co prawda były zakontraktowane 3 poważne zakupy obrabiarek z zachodu, ale nie doszło do realizacji kontraktu, ponieważ ze względu na swoje możliwości techniczne zostały objęte embargiem i zakup sfinalizowano dopiero na początku lat dziewięćdziesiątych – zaznacza Bartnik.
Kierownik sekcji Działu Konstrukcji Narzędzi i Oprzyrządowania w ramach Służby Głównego Technologa, a także I sekretarz Zakładowej Organizacji Partyjnej Roman Lewalski wspomina, że w latach 1987 do 1990 dział konstrukcji oprzyrządowania liczył nie więcej jak 10 osób (w tym personel pomocniczy). – Zadaniem działu było wykonywanie dokumentacji konstrukcyjnej na przyrządy i narzędzia specjalne wg zleceń działu technologicznego. Prace były wykonywane zgodnie z harmonogramem (jak pamiętam, przy dużej liczbie nadgodzin), co wynikało głównie z powodu braków kadrowych – wyjaśnia Lewalski.
Kierownikiem działu Konstrukcji Narzędzi i Oprzyrządowania był Ryszard Rutkowski, wybitny specjalista od konstrukcji narzędzi do obróbki uzębień, zrobił nawet własne oprogramowanie do liczenia tych narzędzi. Skonstruował oprzyrządowanie do dłutowania uzębienia wewnętrznego, a wykonaniem narzędzia zajmowała się służba narzędziowa i jej technolodzy. Jej pracownicy dobierali m.in. materiał i obróbkę cieplną.
Koło planetarne reduktora było dużym elementem i łatwo mogło odkształcić się podczas obróbki cieplnej. – Po rozgrzaniu nawęglonego koła planetarnego do 820 stopni C, wsadzało się w niego trzpień, który odtwarzał uzębienie i taki komplet zanurzaliśmy w wannie z olejem. Nie mieliśmy możliwości szlifowania kół o uzębieniu wewnętrznym. Trzpienie były elementem o dużej średnicy, obrabiane cieplnie, o dokładności wykonania do 0,01-0,02 mm. Trzpień nie dopuszczał do owalizacji koła i chronił część przed skoszeniem się zębów. Trzpień jest elementem precyzyjnym i pracochłonnym: musiał mieć odpowiednią wytrzymałość, sztywność, aby nie ulec deformacji podczas skurczu elementu. Taki trzpień był otworowany, aby zmniejszyć masę materiału (w przeciwnym razie ważyłby pod 20 kg) i pracownik łatwo poradził sobie z nim – podkreśla Bartnik.
Prototypownia uporała się z technologią i przekładnie z reduktorami trafiły do producentów samochodów. Wysyp prototypowych prac nastąpił w latach 80., jednak niewiele z tego nie wyszło. Większość z nich trafiła do prototypowych pojazdów Star i Jelcz, w których prowadzono badania eksploatacyjne. Jednak z uwagi na brak funduszy, skrzynie biegów nie zostały wdrożone do produkcji seryjnej.
T&M nr 5/2024
TekstL Robert Przybylski