Chłodnie z Mielca
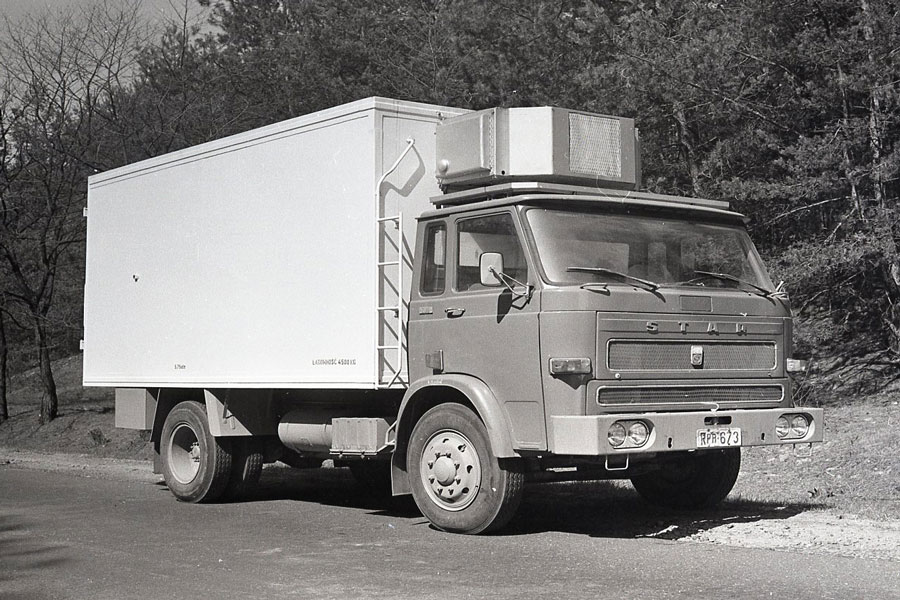
Mielecka Wytwórnia Sprzętu Komunikacyjnego opanowała produkcję samochodowych chłodni.
Zakład przygotował trzy generacje zabudów i dwie generacje sprężarek. Chłodniami woziliśmy półtusze z Opola na szerokotorową stację – wspomina wczesne lata 80 kierowca Opolskich Zakładów Transportu Mięsnego Karol Kasprzyk. – Ćwierci świeże jechały na wisząco, mrożone były wrzucane do środka jak kamienie, na leżąco. Na stacji czekały na nasz towar beczki po 60 litrów, z obejmą, plombowane i z naklejką „farba”. Cała zachodnia strona Polski tam jeździła: z poznańskiego, z opolskiego. W tamtych województwach były mocne PGR-y jak np. Głubczyce – chyba najmocniejszy, hodowlany. Z samego Opola tych chłodni dziennie jechało do przeładunku 5 Jelczy, każdy z przyczepą. Inne zakłady transportu miały czeskie Alki o 20-centymetrowych ścianach. Ich drzwi miały gumowe uszczelki z trzema rzędami ząbków. Gdy drzwi zassały się, nie można było tego otworzyć. Natomiast gdy „uciekał mróz”, pod drzwiami wisiały sople.
Wiszące półtusze bujały samochodem, tak samo ostrożnie i umiejętnie wiozło się bydło. Na suficie wsiało parę ton i trzeba było uważać, żeby tego w rowie nie rozładować. Rond na szczęście wtedy nie było, podobnie jak ślimaków na zjazdach z autostrady – dodaje Kasprzyk.
Pierwsze chłodnie i przepisy
Przewozy chłodnicze należą do stosunkowo młodych rodzajów transportu. Przed wojną ten typ transportu nie był popularny. Pojazdy były chłodzone lodem, a ściany izolowano korkiem lub wiórami. Obieg powietrza wymuszał wentylator napędzany spalinowym silnikiem. Z racji dużej masy zabudowy, chłodnicze przewozy wykonywały przede wszystkim koleje.
Do chłodzenia używany był lód produkowany w lodowniach lub pozyskiwany naturalnie: zimą wyrąbywane na jeziorach i rzekach bloki trzymane były w ziemiankach. Przesypane trocinami potrafiły przetrzymać do jesieni.
Dopiero wynalezienie sprężarkowych chłodni pod koniec lat 30 sprawiło, że lodownie stały się niepotrzebne. Zwiększyła się także ładowność pojazdów. Przewozy chłodnicze upowszechniły się podczas wojny i pokazały branży spożywczej potencjał nowego rozwiązania. Do popularyzacji przewozów chłodniczych przyczyniła się armia USA, która masowo używała takiego taboru dla dostaw żywności.
W Europie było zaledwie tysiąc ciężarówek z nadwoziami chłodzonymi, niemal w całości należącymi do operatorów duńskich i holenderskich. Gdy w latach 50 rząd brytyjski nakazał przewożenie mrożonej ryby wyłącznie chłodniami, firma jednego z niewielkich przewoźników, Herberta Fletchera, pod koniec lat 50 kupiła pierwszą chłodnię z agregatem sprężarkowym. Taka zabudowa kosztowała 2,5 tys. funtów i ważyła blisko 4 tony.
W chłodnictwie Amerykanie byli o krok przed innymi rynkami. W USA już w 1959 roku pojawiły się pierwsze agregaty chłodnicze napędzane silnikiem diesla, który był nawet pięciokrotnie trwalszy od benzynowego i mógł pracować przez 25 tys. godzin.
Jednak to w Europie narodził się międzynarodowy standard przepisów regulujących przewozy chłodnicze. Już w lipcu 1952 roku Europejska Komisja Ekonomiczna ONZ poprosiła Międzynarodową Unię Transportu Drogowego IRU o stworzenie organizacji zrzeszającej przedsiębiorców specjalizujących się w przewozach w temperaturze kontrolowanej, wzorowanej na powołanej w 1949 roku kolejowej organizacji Interfrigo. Politycy i przemysłowcy uważali, że lepiej, aby było to stowarzyszenie przedsiębiorców, a nie organizacja międzynarodowa.
W 1955 roku pod auspicjami IRU przewoźnicy chłodniczy z dziewięciu krajów powołali Transfrigoroute Europe, z siedzibą w Bernie. Założycielami były wiodące przedsiębiorstwa z: Austrii, Belgii, Danii, Francji, Hiszpanii, Holandii, RFN, Szwajcarii i Włoch. Wkrótce dołączyli do nich przedsiębiorcy ze Szwecji. Prezesem został prezes IRU Paul Schweitzer, zaś docelowym zadaniem stało się przygotowanie standardów konstrukcyjnych nadwozi chłodniczych.
Europejski rynek spożywczy
Jednym z pierwszych sukcesów stowarzyszenia Transfrigoroute było wywalczenie pozwoleń na weekendowe przejazdy ciężarówek z żywnością. Zakaz jazdy w niedziele obowiązywał od 1956 roku w Niemczech Zachodnich. Wkrótce podobne ograniczenie wprowadziły Austria oraz niektóre szwajcarskie kantony. Celem regulacji było usunięcie z dróg powolnych ciężarówek i zwiększenie przepustowości arterii.
Przewoźnicy żywności narzekali na powolne działanie punktów odpraw granicznych. Jeden z członków Transfrigoroute wyliczał, że „przejazd z Bretanii do Holandii zajmuje zazwyczaj 3 dni, bo samochód stoi na granicy francuskiej, belgijskiej i holenderskiej czekając na otwarcie biur celników. Taki przejazd powinien trwać niecałe 48 godzin”. Gdy ONZ domagała się od krajów wyjaśnień, rządy jednogłośnie stwierdziły, że robią wszystko co jest w ich mocy, aby przyspieszyć graniczne odprawy.
Tymczasem pomiędzy 1951 i 1960 rokiem import żywności w krajach Europy Zachodniej wzrósł o połowę. W 1960 roku udział żywności sprowadzanej z zagranicy w całkowitej konsumpcji wynosił przeciętnie 14 proc., w tym 5 proc. w przypadku mięsa, 4 proc. jajek, 12 proc. masła i 1 proc. dla serów.
Członkowie Transfrigoroute Europe reprezentowali trzy czwarte rynku przewozów w temperaturze kontrolowanej i z biegiem lat mieli coraz więcej do przewożenia. Produkcja jaj w Europie Zachodniej wzrosła w 1960 roku do 3,4 mln ton, o 42 proc. więcej niż w 1951 roku. W tym samym czasie w Europie Wschodniej produkcja powiększyła się o 44 proc. do 2,3 mln ton. Dla masła wzrosty sięgnęły 29 proc. do 1,8 mln ton dla Europy Zachodniej i 45 proc. dla Wschodniej do 1,3 mln ton. Eksport stanowił jednak niewielki odsetek produkcji. Dla takich firm jak powstałe w 1958 roku PMPS Pekaes, przewozy żywności stanowiły poważną część przychodów.
W kolejnych latach sprawy przygotowania propozycji nowych regulacji wzięły w swoje ręce koncerny spożywcze i sieci fastfoodów. Te firmy szybko rozrastały się w Europie w latach 60 sprzedając w rosnących ilościach mrożoną żywność. Pierwotnie dostawy odbywały się przy pomocy 12-tonowych ciężarówek, jednak okres wysokiej inflacji w latach 70 zachęcił producentów i sieci sprzedaży do otwarcia się na firmy specjalizujące się w logistyce. Przewoźnicy na wynajem chętniej korzystali z coraz większych samochodów, w tym zestawów składających się z ciągnika siodłowego i naczepy chłodni.
W 1980 roku całkowite przewozy produktów żywnościowych w Europie sięgnęły 42 mln ton, w tym ponad 8 mln ton przypadło na mięso, niecałe 8 mln ton na owoce i warzywa i niemal 7 mln ton na banany.
Pierwsze polskie chłodnie
W powojennej Polsce także ruszyły przewozy w temperaturach kontrolowanych, jednak chłodnie były importowane. Dopiero w sierpniu 1960 roku pojawiła się pierwsza chłodnia polskiej produkcji. Zabudowę na podwoziu Star 21 wykonały w pół roku warsztaty Zakładów Transportu Mięsnego w Warszawie. Prototyp miał drewniany szkielet, ale twórca, inż. Połczyński, zamierzał przejść na metalowy. Obciągnięte blachą nadwozie posiadało wymiary wewnętrzne 2x3,4 x1,8m i pojemność 12,2 m3. Izolację stanowił polistyren piankowy.
Wykonany w Tarnowie, ważący 350 kg agregat sprężarkowy był napędzany z przystawki odbioru mocy, a na postoju z sieci; zapewniał utrzymanie różnicy temperatur 40-45 stopni.
Trzytonowe auto oceniała Centrala Przemysłu Mięsnego i pochwaliła automatyczną regulację temperatury w czasie postoju. Konstruktor zaopatrzył pojazd w sygnalizację ciśnienia w parowniku oraz sygnalizację z termostatem działającą w czasie jazdy.
Własna konstrukcja uwalniała kraj od importu, na który nie było dewiz, jednak nie do pomyślenia była produkcja nadwozi w warsztatach przewoźnika. Rząd musiał znaleźć fabrykę z prawdziwego zdarzenia i wybór padł na WSK Mielec, która po zawieszeniu wojskowych zamówień na samoloty nie miała zbyt dużo pracy.
W Mielcu, pod okiem Jerzego Dębickiego, powstał projekt chłodni na podwoziu 8-tonowej ciężarówki Żubr. Prototyp z agregatem francuskiej firmy Termobil gotów był w 1961 roku.
Po krótkich próbach WSK Mielec rozpoczął produkcję chłodni w kolejnym roku. Seryjny Żubr z 5,5-tonową nośnością i nadwoziem o pojemności 21 m3 otrzymał brytyjski silnik oraz agregat sprężarkowy Petter na licencji Thermo King.
Nadwozie otrzymało aluminiowe, wewnętrzne i zewnętrzne poszycie rozpięte na stalowym szkielecie. Styropianowa izolacja miała 15 cm grubości.
Importowane silniki oraz sprężarki były na tyle kosztowne, że produkcja była niewielka. Tymczasem Ministerstwo Przemysłu Spożywczego i Skupu domagało się pilnych i licznych dostaw samochodów chłodniczych, na co Komisja Planowania wysupłała pieniądze. Ministerstwo Przemysłu Ciężkiego zleciło przygotowanie produkcji sprężarek w WSK Mielec oraz rozwinięcie w tejże fabryce Wydziału 62, specjalizującego się w budowie zabudów chłodniczych.
Konstruktorzy zdobywali doświadczenie na kolejnych modelach samochodów-chłodni. W 1965 roku światło dzienne ujrzały prototypy samochodu-chłodni Ms-2,5 (Ms od Mielec - samochód) na podwoziu Stara 25L.
Produkcja tego modelu o ładowności 2,5 tony ruszyła w 1967 roku, podobnie jak agregatu.
Zjednoczenie Przemysłu Motoryzacyjnego planowało w 1968 roku, że na nowych 6- i 10-tonowych podwoziach Zjednoczenie Przemysłu Lotniczego (w którym znajdowała się WSK Mielec) będzie produkować 320 chłodni rocznie.
Utajnione silniki
Kamieniem milowym w opanowaniu produkcji samochodów chłodniczych krajowej konstrukcji było przygotowanie przez WSK Mielec agregatu ziębniczego BS-4SE własnej konstrukcji. Do jego napędu konstruktorzy wybrali 5-konny, 1-cylindrowy, chłodzony powietrzem benzynowy silnik S101-M-1B produkcji Zakładów Sprzętu Motoryzacyjnego Nr 1 w Łodzi.
Było to rozwiązanie dobre, bo polskie, a S101M przy wszystkich jego wadach, jeśli tylko zadbany, był niewiarygodnie trwały. Wytrzymywał 2000 godzin pracy pod obciążeniem. – Nie wiem kto wykonał adaptację dokumentacji konstrukcyjnej. Może inż. Edmund Lisiak wespół z Leszkiem Boryną, a może inż. Patora (ojciec wersji S101M) zanim odszedł z ZSM Nr 1 do ZM im. Strzelczyka? Gdy przyszedłem do pracy w FOS Polmo (kolejna nazwa ZSM nr 1), już robiono silniki z dodanym wieńcem rozrusznika z koła zamachowego silnika S31, rozrusznikiem z tegoż silnika oraz membranową pompą paliwa (typu 0.20 z silnika M20 lub S21) napędzaną z prymitywnej przystawki zawierającej krzywkę, ulokowanej w miejscu, w którym w standardowym silniku był zespół rozrusznika na pasek oraz tłumiku wydechu z wylotem do góry – opisuje silnik Andrzej Pertyński, który w latach 80 był głównym konstruktorem Fabryki Osprzętu Samochodowego Polmo.
Wojsko miało powyżej uszu problemów z produkowanymi na radzieckiej licencji silnikami rodziny Ł. Ministerstwo Przemysłu Ciężkiego zleciło w 1956 roku Wytwórni Sprzętu Mechanicznego w Łodzi (wcześniejsza nazwa ZSM Nr 1) opracowanie silnika do agregatu 2,2 kW, koniecznie benzynowego i chłodzonego powietrzem. – Tu do roboty bierze się Mates Heilig, który co prawda już nie pracuje w WSM, ale jest konsultantem z Katedry Silników Spalinowych Politechniki Łódzkiej i to on kieruje pracą narzucając jej kierunek, gdyż przynosi w skrzynce po jabłkach rozmontowany silnik 985 cm3 samochodu KdF Typ 81. Zbożne kopiowanie daje szybkie efekty, powstaje prototyp, nikt nie przejmuje się tym, że na badania trwałościowe nie ma czasu, MON przyjmuje projekt i powstaje gruby problem, technologia – opisuje Pertyński.
Podkreśla, że produkcja S101 była mocno rozkooperowana. – Tłoki z Gorzyc, tuleje z Kalisza, odlewy kadłuba dostarczał Nowotko, odkuwki korbowodu i wału korbowego za moich czasów przyjeżdżały z FSC Lublin, a wcześniej nie wiem. Staliwne koło zamachowe z wieńcem łopatek dmuchawy chłodzącej silnik odlewały początkowo ZM im. Strzelczyka, później ktoś przyciśnięty odlał tych kół z tysiąc i leżały sobie w magazynie, cewka iskrownika pochodziła z warszawskiego Zelmotu, odlewy korpusów gaźników K12 z POM pod Pabianicami, którego nazwy nie mogę sobie przypomnieć, jedno tylko pamiętam: wszystkie maszyny produkowane przez ten POM były zielone – wspomina Pertyński.
Produkcja była silnika niewielka, więc nie było mowy o specjalistycznych maszynach: do dyspozycji były jedynie tokarki i frezarki uniwersalne i umiejętności oraz siła robotników. Pertyński podkreśla, że S101 należał do produkcji „S” (nie istniała taka pozycja w cenniku wyrobów fabryki) i przytacza wspomnienia wieloletniego pracownika biura konstrukcyjnego ZSM Nr 1 inż. Leszka Katuszewskiego. – Tajność była taka, że robotnikowi wykonującemu jakąś operację obróbki nie wolno było mieć rysunku obrabianej części. Pan Katuszewski nie byłby sobą, gdyby nie zakpił z durnego systemu: zlecił prototypowni wykonanie blaszanych skrzyneczek zamykanych na kłódeczkę, a skrzyneczki te zostały zamocowane do pasów, którymi opasali się robotnicy, dostali kluczyki do kłódeczek i mogli mieć przy sobie rysunki wykonywanych przez siebie części. Uśmiech na twarzy pana Katuszewskiego świadczył, że cieszył się tym bardzo, iż żart został przez panów ze 111 Przedstawicielstwa Wojskowego przyjęty poważnie! – cytuje Pertyński.
Zaznacza, że pierwszy S101 jeszcze bez M, miał panewki (zapewne z Bimetu) i żyły one w silniku krótko. – Silniki lubiły się zacierać, o ile wcześniej regulator obrotów (przeniesiony z silnika Ł 3/2) nie wykończył lamp w radiostacjach, gdyż niestarannie wykonany (różne masy ciężarków) regulator nie trzymał nakazanej i wynikającej z częstotliwości 50 Hz prądu zmiennego prędkości obrotowej 3000 obr/min. Wybuchła duża chryja i w 1960 roku pośpiesznie silnik zmodernizowano, zastępując łożyska ślizgowe tocznymi (rolkowymi na wale korbowym i igiełkowym w główce korbowodu), rozrusznik na korbę łamiącą palce żołnierzom zastąpiono paskiem nawijanym na kółko zamocowane na przednim czopie wału korbowego – wylicza Pertyński. – Wynik końcowy, czyli S101M miał masę 44 kg, co w porównaniu do ważącego 92 kg Ł 3/2 było osiągnięciem na owe czasy sporym – podkreśla główny konstruktor FOS Polmo.
Gdy silnik już przechorował pierwsze choroby wieku dziecinnego i został zmodernizowany do poziomu S101M, wojsko nie chciało innego, lepszego i nowocześniejszego. – Utyskiwali ciągle na parametry silnika, ale nie chcieli nowej konstrukcji, a bez ich poparcia nie byłoby środków na opracowanie konstrukcji i uruchomienie produkcji – przyznaje Pertyński.
Gierkowski boom
28 maja 1969 roku dyrekcja WSK Mielec powołała Zakład Doświadczalny. W pierwszym roku istnienia Wydział Budowy Prototypów Zakładu Doświadczalnego zbudował prototypy chłodni Ms-3 i Ms-5 na podwoziach (odpowiednio) Stara 29 i Jelcza 315. Produkcja obu zabudów ruszyła w 1970 roku, oba otrzymały agregat ziębniczy BS-4SE.
Komitet Transportu Wewnętrznego EKG ONZ założył, że w najwyższej grupie urządzeń chłodniczych temperatura w komorze chłodniczej może być dowolnie wybierana w przedziale od – 20 do + 12 st. C, a zabudowa utrzyma ją nawet przez 12 godzin przy temperaturze zewnętrznej +30 st. C.
Komisja ustaliła graniczny współczynnik przenikania ciepła, jednak polskie zabudowy nie spełniały normy z powodu zastosowania metalowej ramy.
Krajowy przemysł chemiczny nie dysponował materiałami, które zapewniłyby odpowiednią izolację, więc pozostało opracować sprawniejsze sprężarki. Konstruktorzy OBR SK (w 1972 roku dyrekcja fabryki przekształciła ZD w OBR Sprzętu Komunikacyjnego) opracowali nowy agregat BS-5 o wydajności 2500 kcal/godz., blisko dwa razy wyższej od poprzedniego agregatu. Dla chłodni na Jelczu pozwolił na mrożenie do 18 st. C. Pierwsza seria pojawiła się w 1973 roku po próbach przeprowadzonych w Centralnym Ośrodku Chłodnictwa w Krakowie.
Dwa lata później konstruktorzy OBR SK odpowiadając na apel władz państwowych, w ramach „Powszechnego Przeglądu Konstrukcji i Technologii” przeprowadzili gruntowną rekonstrukcję samochodów chłodni Ms-3 i Ms-5.
Tylko w wyniku rekonstrukcji technologii modelu Ms-3 zakład oszczędził 120 ton stali, 23 tony materiałów kolorowych i 82 m3 drewna w stosunku rocznym oraz 150 tys. godzin obniżki pracochłonności w stosunku rocznym. Dodatkową korzyścią było zwiększenie trwałości np. podłogi.
W 1975 roku Wydział 62 zbudował 1254 chłodnie, o 32 proc. więcej niż w 1974 roku. W kolejnym roku wydział przystąpił do budowy polsko-belgijskich naczep chłodniczych, 16-tonowych na standardowym podwoziu naczepy D-18 produkcji ZREMB Wrocław. Komora chłodnicza wykonana została całkowicie z tworzyw sztucznych z izolacją poliuretanową. Dostawcą nowej dla wydziału technologii klejenia była belgijska firma Baeten. W pierwszej serii powstało 10 naczep-chłodni, które trafiły do Warszawy i Opola.
W 1975 roku dyrekcja Wytwórni Urządzeń Chłodniczych w Dębicy wystąpiła do dyrekcji WSK Mielec z wnioskiem o podjęcie produkcji przyczep w kooperacji. Na zamówienie WUCh konstruktorzy opracowali dokumentację 8-tonowej przyczepy chłodniczej Ms-14. Odpowiada ona kształtem i wyglądem nadwozi Ms-5. Uruchomienie produkcji tej przyczepy wymagało wykonania kosztownego i czasochłonnego oprzyrządowania, więc konstruktorzy zaproponowali wykorzystanie elementów zabudowy Ms-3. OBR SK przygotowało dokumentację wykonawczą na przyczepę Ms-14A.
Jej prototyp został wykonany w styczniu 1976 roku, z agregatem BS-4SE produkcji WSK Mielec. WUCH Dębica przeprowadziło badania cieplne, wytrzymałościowe i eksploatacyjne prototypu. Produkcja ruszyła w kolejnym roku.
Powszechne przewozy chłodnicze
Polska podpisała w 1984 roku umowę ATP o międzynarodowych przewozach szybko psujących się artykułów żywnościowych i o środkach transportu przeznaczonych do tych przewozów.
Po kraju jeździło blisko 10 tys. chłodni. – Krajowy sprzęt nie był trwały. W tych czasach ze wszystkim było słabo, kierowca dostawał premię za 100 tys. przebiegu. W silnikach benzynowych zapłon sam się przestawiał i trzeba był mieć na niego oko. Silniki były głośne, gdy pracowały trudno było zasnąć w kabinie. Jednak zabudowy były solidne, stabilniejsze od dzisiejszych. Musiałem nie raz się naszarpać, aby otworzyć drzwi. Szczególnie jak zassało powietrza, musiałem podważyć skrzydło drzwi, żeby wpuścić powietrze – opisuje Kasprzyk.
Natomiast dyrektor ds. technicznych Spółdzielni Transportu Wiejskiego w Radomiu Ryszard Kosałkiewicz wspomina, że agregat wymagał pracochłonnej obsługi. – Chłodnia często odwiedzała stację obsługi, w której wymieniano freon. Na szczęście nie miałem przypadku, aby silnik lub agregat zepsuł się. Zawsze dowieźliśmy ładunek – zapewnia Kosałkiewicz.
Podziękowania dla: Janusza Halisza, Ryszarda Kosałkiewicza, Karola Krawczyka, Andrzeja Pertyńskiego.
T&M nr 3/2022
Tekst: Robert Przybylski
Zdjęcia: Muzeum Historii Fotografii „Jadernówka” w Mielcu