Niespełniona licencja
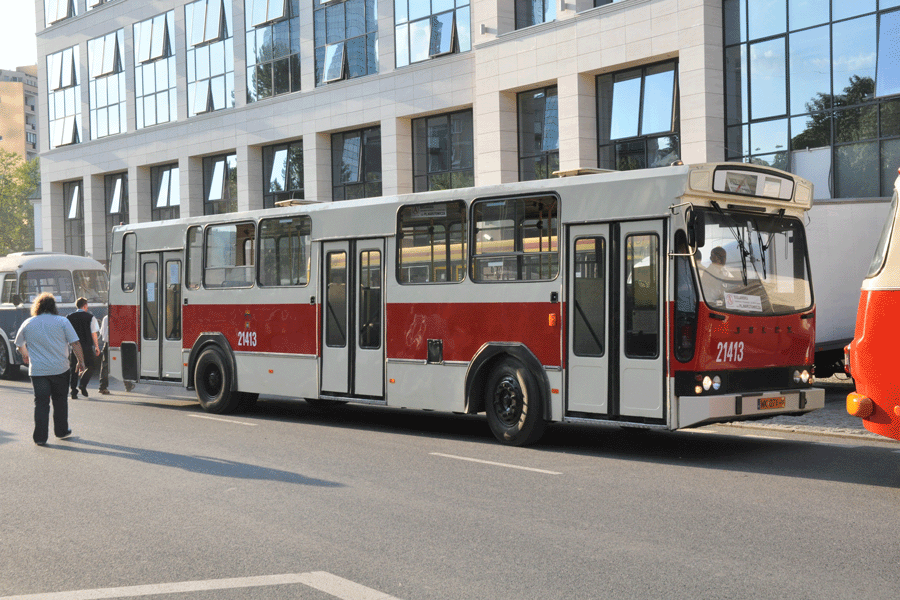
Na pełne wdrożenie licencji Berlieta zabrakło pieniędzy, a warta 4,5 mld zł inwestycja w JZS nie przyniosła oczekiwanych rezultatów.
Po podpisaniu 1 sierpnia 1972 umowy licencyjnej z Berlietem, przed Jelczańskimi Zakładami Samochodowymi stanęło poważne zadanie inwestycyjne, które w zasadniczy sposób zmieniło pracę dyrekcji przedsiębiorstwa. – Oprócz nadzorowania normalnej pracy produkcyjnej musieliśmy realizować wielką inwestycję zarówno w zakresie budowlanym jak również technologicznym – wyjaśnia zastępca dyrektora JZS ds. produkcji w latach 1971 – 1977 Jerzy Podlak.
Dyrekcja przedsiębiorstwa postanowiła utworzyć cztery zakłady, nadając ich kierownikom duży zakres samodzielności oraz odpowiedzialności z wyłączeniem spraw ekonomicznych. – Należy pamiętać, że poszczególne zakłady zatrudniały po kilkaset ludzi, a więc były to małe przedsiębiorstwa. Dyrektor produkcji zamiast 21 podmiotów nadzorował 4. Praktyka późniejszych lat potwierdziła celowość tej decyzji i obowiązywała ona do chwili upadku JZS – podkreśla Podlak.
Najnowsze maszyny
Wraz z licencją JZS wzbogaciły się m.in. o 400 obrabiarek w Hali B, francuskie prasy podwójnego działania Bliss ustawione w tłoczni w Hali A, centralną mieszalnię farb, lakiernię kabin ciężarówek w Hali C, nową Halę E z kompletnym ciągiem technologicznym produkcji autobusów na licencji Berlieta: od spawania kratownic, poprzez spawanie poszycia po lakierowanie i wyposażenie.
– Berliet pełnił rolę głównego dostawcy maszyn i urządzeń, dzięki czemu udało się obejść zakaz eksportu różnych maszyn do krajów RWPG – podkreślał główny inżynier JZS Henryk Orzechowski. Berliet zobowiązał się do pomocy przy zaprojektowaniu zakładu zdolnego do produkcji nie tylko 5 tys. autobusów rocznie, ale i 20 tys. zawieszeń przednich, 20 tys. tylnych mostów i 20 tys. foteli kierowcy, przewidzianych do stosowania także w innych pojazdach.
- Kupując Blissy myśleliśmy nie tylko o autobusach, ale o całym asortymencie produkcji. Pamiętać należy, że Erfurty były już wyeksploatowane, mieliśmy problemy z częściami zamiennymi (jak to w krajach RWPG bywało). Sam z racji znajomości języka niemieckiego jeździłem z przedstawicielami działu Głównego Mechanika do Erfurtu ze skrzynką polskiej wódki i innymi gadżetami by dostać niezbędne części – wspomina Podlak.
Podkreśla, że modernizacja wyposażenia nakładała się na prace budowlane, czyli wznoszenie hal produkcyjnych. Z tego samego funduszu finansowano budowę szkół, ośrodka wypoczynkowego w Mielnie i osiedli mieszkaniowych, początkowo w Oławie, a po kryzysie paliwowym z roku 1976 także w Laskowicach. – W tę drugą kwestię zaangażowana była fabryka, bo mieszkania powstawały głównie dla kadry inżynierskiej i robotników zatrudnianych w JZS. Wszystkie te działania miały przynieść wzrost produkcji, dlatego obok codziennego kierowania tym pionem, musiałem nadzorować i koordynować także działania inwestycyjne. W JZS następował wtedy stały przyrost produkcji. W 1970 roku fabrykę opuściło 7328 pojazdów, a w 1976 już prawie 12 tysięcy – porównuje zastępca dyrektora JZS ds. produkcji.
Rekordy narzędziowni
Zanim produkcja Jelcza wzrosła o prawie dwie trzecie, pracowników zakładu czekał spory wysiłek. W porozumieniu licencyjnym strony uzgodniły, że po 24 miesiącach od złożenia podpisów, Berliet zacznie przesyłać do Jelcza standardy montażowe modelu PR 110U, zaś kompletne wyposażenie JZS Jelcz do produkcji autobusów miejskich będzie gotowe 32 miesiące po podpisaniu kontraktu, w kwietniu 1975 roku. W tym tempie musieli pracować nie tylko konstruktorzy Berlieta, ale i jelczańskie służby.
Tymczasem do autobusu potrzeba było przygotować 8893 pozycje oprzyrządowania specjalnego dla 1355 maszyn. Dla produkcji Berlieta wykonano 10,5 tys. rozmaitych przyrządów, co pochłonęło 4,5 mln roboczogodzin. Produkcja globalna narzędziowni wzrosła z 580 tys. godzin w 1972 roku do 800 tys. dwa lata później i przekroczyła milion w 1976 roku, aby w 1980 dojść do 1160 tys. godzin.
Zastępca dyrektora ds. inwestycji JZS Edmund Orłowski tłumaczył w marcu 1975 roku, że Berliet nieterminowo dostarcza do Motoprojektu założenia do projektów branżowych. Motoprojekt koordynował cały projekt rozbudowy zakładu, zamawiał nawet niektóre maszyny, a resztę kupował Metalexport. – Bez Motoprojektu nic byśmy nie zrobili. Oni mieli doświadczenie w projektowaniu zakładów motoryzacyjnych, a we Wrocławiu nie było takich specjalistów – oceniał Orzechowski.
Opóźnienia Berlieta wynosiły od 6 do 12 miesięcy. Z tego powodu np. ZUGiL Wieluń nie mógł zaprojektować lakierni w Hali E, a główny wykonawca, czyli Wrocławskie Przedsiębiorstwo Budownictwa Przemysłowego nr 1, nie mogło rozpocząć kopania wykopów pod fundamenty. Szybciej, bo 11 maja 1976 roku, przedstawiciele producenta francuskich pras Bliss przekazali maszyny Jelczowi.
Jelcz PR 110U był montowany w formułach, podobnie jak PR 100 w fazach. – Zaczęliśmy małą ilością autobusów od formuły B (autobus przyjeżdżał na kołach, w Jelczu uzupełniano wnętrze o siedzenia, poręcze etc. oraz malowano czerwone pasy). W końcu 1975 roku ruszył montaż w formule C, w której w skrzyniach przychodziły z Lyonu kratownice i szkielety ścian oraz dachów, natomiast silniki i skrzynie biegów od polskich dostawców (Mielec i Tczew). Opanowanie produkcji PR 110U przebiegało sprawniej niż PR 100 – zapewnia odpowiedzialny za technologię zabezpieczenia antykorozyjnego w JZS Wiesław Cieśla.
Montaż odbywał się w Hali A, natomiast lakierowanie w Hali F, w zbudowanej w latach 60 lakierni autobusów na licencji Karosy i nadwozi wojskowych. W 1975 roku zakład opuściła seria informacyjna siedemnastu PR 110U. Miały poszycie z nitowanych sekcji, podobnie jak PR 100. Umowa licencyjna przewidywała wyprodukowanie w 1975 roku 510 autobusów PR 110U, z tego 133 z niemal 72-procentowym udziałem komponentów krajowych, a 377 z ponad 87-procentowym udziałem.
W fazie D i E szkielety elementów nadwozia, łącznie z kratownicą, były już od podstaw wykonywane w Jelczu. 2 sierpnia 1976 roku nastąpił rozruch linii spawalniczej zespołów i szkieletów autobusów licencyjnych w Hali E. 14 września 1976 roku z JZS wyjechał pierwszy seryjny, całkowicie wykonany w kraju Jelcz PR 110U.
Pełen proces technologiczny w Hali E ruszył dopiero w grudniu 1978 roku, po trzykrotnym przesuwaniu terminu. Produkcja mogła sięgnąć 5 tys. autobusów, 3 tys. tylnych mostów oraz tysiąca zawieszeń przednich rocznie. Inwestycja w maszyny sięgnęła 80 mln francuskich franków. Berliet złożył gwarancję bankową w wysokości 10 proc. ogólnej wartości maszyn i urządzeń, że fabryka będzie w stanie produkować do 5 tys. autobusów rocznie.
Nowoczesne wyposażenie widoczne było m.in. na linii szkieletu PR 110U w Hali E, gdzie na koniec 1981 roku działało 414 automatów spawalniczych, 325 zgrzewarek oporowych i 5 automatów spawalniczo-zgrzewalniczych. Francuski robot ARO zgrzewał poszycie drzwi wszystkich rodzajów autobusów.
Bieda dostawców
Pełnomocnik dyrektora naczelnego Przedsiębiorstwa Handlu Zagranicznego Przemysłu Motoryzacyjnego Pol-Mot ds. licencji autobusu Czesław Koskowski został szefem delegatury Pol-Mot w Lyonie. – Najważniejszym zadaniem było przejęcie dokumentacji, dlatego moim zastępcą był główny konstruktor JZS Jan Walas. Część dokumentacji odnosiła się do konstrukcji bazowej (PR 100), a część była tworzona specjalnie dla nas (PR 110U). Razem z francuskimi kolegami wykonaliśmy przez parę lat ogromną robotę, sprawdzając, czy kolejne transze rysunków są kompletne i spójne z wcześniejszą dokumentacją. Drugim zadaniem była obsługa handlowa i poprowadzenie sublicencji na różne komponenty, łącznie kilkadziesiąt pozycji – wspomina Koskowski.
Wraz z licencją na Berlieta, Pol-Mot musiał zakupić sublicencje m.in. na wspomagany hydraulicznie mechanizm kierowniczy ZF, koła włoskiej firmy G. Gianetti (Fergat), opony (rozmiar 10.00R20) od Uniroyal Englebert, wiązki elektryczne, materiały cierne, zamki, okna a nawet podkładki i nakrętki.
W zależności od wersji w autobusie znajdowało się od 599 do 658 pozycji, których nie produkował Berliet. Większość z nich – według oświadczenia Berlieta – nie była chroniona patentami. Do 112 części wartych 5 tys. franków (tysiąc dol.) na autobus i do tego łożysk wartych 440 franków (90 dol.) na autobus, nie było jasności co do patentów czy praw własności przemysłowej.
Berliet zobowiązał się zbadać sprawę w 3 miesiące od podpisania umowy. W Polsce należało podjąć produkcję od szesnastu do osiemnastu części. Do dziesięciu pozycji Berliet wykupił prawa i przekazał Polsce, w tym na sprężyny śrubowe, wały napędowe, mechanizm hamulca przedniego, drzwi składane kompletne autobusu miejskiego, drążki kompletne układu kierowniczego, koła kierownicy i mechanizm zawieszenia siedzenia kierowcy. Pol-Mot przewidywał import m.in. miechów powietrznych, wskaźników i czujników oraz oświetlenia jarzeniowego.
Kooperanci ze Zjednoczenia Przemysłu Motoryzacyjnego mieli dostarczać do JZS 298 pozycji, przedsiębiorstwa podległe Ministerstwu Przemysłu Maszynowego 228, a z innych resortów 731 pozycji. Rada Ministrów podjęła 6 lipca 1973 roku uchwałę nr 162/73, która ostatecznie zadecydowała o rozpoczęciu produkcji autobusów licencyjnych. Uchwała i jej rozporządzenia wykonawcze ustalała zadania dla poszczególnych resortów i zakładów przemysłowych.
Dostawcy mieli początkowo otrzymać 0,94 mld zł, po czym rząd obciął fundusze do 0,6 mld zł, zaś ostatecznie przekazał 0,32 mld zł. W rezultacie kooperanci nie potwierdzili dostaw 271 pozycji z łącznej liczby 1257, co zmusiło JZS do produkcji wielu zespołów we własnym zakresie. – Zmorą naszego przemysłu motoryzacyjnego było niedoinwestowanie zakładów kooperacyjnych co miało ogromny wpływ na brak rytmiczności dostaw. Problem nasilił się szczególnie w drugiej połowie lat siedemdziesiątych. Były nadgodziny, było stałe gonienie planu – opisuje Podlak.
Pomimo kłopotów dostawców, 1 kwietnia 1976 roku centralna tłocznia Kieleckiej Fabryki Samochodów Specjalizowanych Polmo-SHL zakończyła produkcję pierwszej partii kompletnych wytłoczek dla firmy Berliet. Fabryka produkowała 20 rodzajów wytłoczek dla tego odbiorcy.
Druga transza finansowania
WSK Mielec zamiast 5 tys. silników dostarczała tysiąc-dwa, brakowało także uszczelek ze Stomil Sanok, odkuwek z Huty Stalowa Wola i odlewów z FSC Lublin. Produkcja tylnych mostów i przednich osi miała ruszyć w 1975 roku. Dopiero rok później udało się znaleźć dostawcę kół talerzowych do tylnych mostów (Zakłady Mechaniczne Glimag w Gliwicach), który rozpoczął ich produkcję w 1977 roku.
Cena eksportowanego do Francji tylnego mostu wyniosła 5650 franków francuskich, a przedniej osi 4429 franków. Obok kratownicy były to podstawowe komponenty, którymi Polska miała spłacić licencję. Umowa licencyjna objęła dostawami 82 wyroby i materiały z Polski, w tym tylne mosty, wały napędowe, niezależne zawieszenie przednie, autobusy i autokary niekompletne, okna kierowcy, bezpieczeństwa i uchylne, łożyska, narzędzia skrawające, elementy nadwozia, kratownice, samochody ciężarowe Star, części silnikowe, skrzynie biegów, układu hamulcowego, układy kierownicze, kierownice typu Star.
Łączna wartość komponentów dostarczonych przez Pol-Mot do Berlieta miała sięgnąć 207,3 mln franków (41 mln dol.). Natomiast łączny koszt licencji i zakupów kooperacyjnych miał wynieść 332 mln franków, czyli 66,4 mln dol.
Opóźnienia rosły, natomiast administracyjne naciski na dostawców niewiele dawały. Wiesław Cieśla pamięta jedno ze spotkań w 1980 lub 1981 roku, które prowadził wiceminister przemysłu maszynowego Andrzej Jedynak, poświęcone wdrożeniu uchwały Prezydium Rządu dotyczącej uruchomienia produkcji Berlieta. Każdy z zaproszonych meldował sposób wdrożenia uchwały. Jeden z dyrektorów zjednoczenia produkcji śrub opisał jakich dokonał uruchomień. Przyznał, że zjednoczenie nie rozpoczęło produkcji kilku rozmiarów śrub, bo „zapotrzebowanie Jelcza jest tak małe, że to nie ma sensu”. Na to zdenerwowany wiceminister Jedynak podniósł się zza stołu i powiedział: „Nie jesteśmy tu od tego czy coś ma sens czy go nie ma, tylko od sprawozdania z wprowadzenia w życie uchwały rządu”.
Rząd planował, że dostawcy JZS otrzymają brakujące fundusze przy okazji podpisanej w 1975 roku licencji Steyra, której zakończenie wdrożenia przewidywał na 1983 rok, jednak zawiesił późną jesienią 1980 roku.
Państwowa kasa była pusta: na koniec 1980 roku zagraniczne zadłużenie kraju sięgało 60 proc. PKB i 5-krotnie przekraczało roczne wpływy z eksportu. Sam koszt obsługi długu sięgnął 10 proc. PKB i 80-90 proc. wpływów z eksportu, natomiast odsetki wyniosły 5 proc. PKB i 40 proc. wpływów z eksportu.
Z powodu wstrzymania finansowania, linie oblachowania zewnętrznego w JZS pozostały niekompletne, nie starczyło funduszy na lakiernię proszkową i lakiernię mostów napędowych oraz na ekspedycję samochodów. Faktyczne moce produkcyjne zmalały z 5 tys. autobusów do 3,5 tys.
Garb zadłużenia
Łącznie za licencję na autobusy i mosty napędowe Polska zapłaciła 34 mln franków, czyli 6,8 mln dol., przy 5-procentowej zaliczce i reszcie rozłożonej na 5 lat przy oprocentowaniu całości 3 proc.
Import kooperacyjny przewidziany na lata 1972-1980 został wyceniony na 218 mln franków (43,6 mln dol.), z którego 85 proc. wartości było płacone w 5-letnim kredycie kosztującym 6,3 proc. rocznie, zaś import inwestycyjny wynosić miał 80 mln franków (16 mln dol.) z którego 85 proc. wartości było w kredycie oprocentowanym na 6,7 proc.
Nakłady na modernizację JZS wyniosły 3,97 mld zł, z tego na roboty budowlano-montażowe władze państwa przeznaczyły 1,34 mld zł. JZS zmodernizowały tłocznię w Hali A, wydział obróbki wiórowej w Hali B, lakiernię kabin w Hali C, stworzyły wydział kratownic w Hali D oraz wzniosły rozebraną tuż po wonie przez Armię Czerwoną Halę E, w której znajdowały się spawalnia, montaż i lakiernia autobusu licencyjnego. Z tej puli zakład wybudował w okolicy kilka szkół, osiedli mieszkaniowych i ośrodek wypoczynkowy w Mielnie.
Jednak 4,5 mld zł na inwestycje było formalnie pożyczką, którą JZS musiały zwrócić do NBP.
Od początku 1978 roku Jelcz co roku z tytułu spłaty inwestycji licencyjnej odprowadzał do NBP miliard złotych. W 1980 roku spłacił zadłużenie dewizowe, a w połowie 1982 roku JZS spłacił całość kredytu.
Główny negocjator licencji Jelcza Czesław Koskowski potwierdza, że według jego wiedzy zostało spłacone wszystko, za wyjątkiem różnych drobiazgów. – Berliet zaliczył kilka spóźnień i Pol-Mot wynegocjował obniżenie niektórych opłat dla Francuzów. Berliet został spłacony i generalnie wszystko przebiegło zgodnie z umową. Natomiast nie wypalił eksport kompensacyjny do Lyonu – przyznaje Koskowski. Tłumaczy, że produkcja komponentów objęła mały zakres, winne były opóźnienia w uruchamianiu produkcji, jej niedostateczna jakość oraz liczne reklamacje.
Dyrektor Podlak dodaje, że Francuzi byli zaskoczeni jak szybko spawacze Jelcza opanowali spawanie konstrukcji kratownic, które były eksportowane do Lyonu i stanowiły jeden z głównych komponentów eksportu. – Oczywiście były pewne sprawy jakościowe, ale nie odbiegały one od ogólnych norm i na pewno nie były powodem klęski Jelcza – zapewnia Podlak.
Podziękowania dla: Wiesława Cieśli, Czesława Koskowskiego, Jerzego Oleńczaka, Henryka Orzechowskiego, Jerzego Podlaka.
T&M nr 6/2019
Tekst: Robert Przybylski